It is a process of treating the soil to improve its stability and bearing capacity for using soil Stabilization as Construction materials. This is a method of changing the soil properties by the use of controlled compaction, proportioning or the addition of suitable admixtures.
Purpose: Stabilization of soil is practiced in road construction for one or more of the following objectives:
- To bring economy in roads construction.
- To increase the strength of pavement layers like sub-bases, base courses, etc.
- To alter permeability characteristics.
- To reduce compressibility and settlement reduce frost susceptibility.
- To increase the stability of earthworks in embankment as a whole.
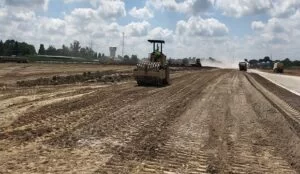
Types of Soil Stabilization
Following are the commonly used methods of types soil stabilization:
1. Mechanical Stabilization
2. Cement Stabilization
3. Lime stabilization
4. Bitumen Stabilization
1. Mechanical Stabilization: It involves Iwo operations:
a. Changing the composition of soil by addition or removal of certain constituents.
b. Densification or compaction.
The stability of granular soil having a negligible amount of fines can be increased by mixing with a certain proportion of binder soil.
Similarly, the stability of fine-grained could be improved by mixing a suitable proportion of granular materials.
For Mechanical stabilization, where the primary the primary purpose is to have a soil-resistant to deformation and displacement under loads, soil material can be divided into two fractions, the granular fraction and fine soil fraction.
The granular fraction provides strength and hardness.
The fine fraction provides cohesion, water retention capacity and also acts as filler.
If the soil collected from one source does not meet the gradation and plasticity requirements of a job, it becomes necessary to mix material from more sources for obtaining the desired mixtures.
The blending of materials is done by making a trial combination.
Construction Procedures
The material are collected from the selected roadside borrow pits and stacked along the side of the road.
The materials collected are mixed to desired proportions and the water contents of the mixture are determined by rapid method. If required water is added to the mixture.
The wet mixture is then spread on the prepared Sub-grade to the desired grade and compacted by using 8 to 10 tones three-wheeled rollers.
Rolling is continued till adequate compaction is achieved. The surface Mix-cement is then allowed to dry and opened to traffic after drying.
What is soil stabilization? Type of soil Stabilization?
Discuss the Cement Stabilization of soil including its construction procedure.
The cementing action results from the chemical reaction of cement with silica contents of soil during hydration.
In coarse-grained soils, the mechanism of stabilizing is due to the development of bonds at the point of contact of hydrate cement and compacted soil particles.
In fine-grained cohesive soils, the cement stabilization is due to the reduction of plasticity and formation of matrix enclosing clay lumps.
Soil cement can be used as a sub-base or base course of all types of pavement.
Construction Procedure
Following are the construction steps for soil-cement bases:
1) Preparing the subgrade
2) Pulverizing the soil
3) Adding and mixing cement
4) Adding and mixing water
5) Compacting
6) Finishing
There are two methods of construction:
a. Mix-in-Place method
b. Plant-mix method
Traveling plant method
Stationary plant method
In the Mix-in-place method, the prepared subgrades is scratched to the required depth of treatment and the soil is pulverized until at least 80% of the soil passes a 4.75 mm sieve. If any blending of soil is needed, it is done with the loose and pulverized soil.
The pulverized soil is then mixed with the required amount of cement and mixed properly. The required quantity of water is then added to the mixture and mixing is continued. The wet mixing operation should not continue for more than 3 hours.
The wet mixture is then spread and shaped to the proper grade. After compaction is done by using 6 to 10 tones roller. The compacted soil-cement surface is cured for 7 days and is opened for traffic.
In-plant mix method, large mixing plants are used for mixing soil, cement, and water. The mixture is then spread on prepared on the prepared subgrade to the required grade and compacted.
What is Bituminous Macadam? Discuss methods of its construction.
This is also called bitumen’s bound macadam’s. It consists of a single layer of compacted crushed aggregates premixed with a bituminous binder.
The thickness of this type of base .course is 50mmor 75mm this provides an economical and string base course.
The load distribution through bituminous macadam is on a wider area and is more resistant to deformation.
Hence a thin layer of this type of base course is equivalent to a thick layer of WBM, It can be used in regions of the high water tables, In snow-bound hilly terrain, and in places where the medium types of aggregates are available.
Methods of construction
Preparation of mix: The binder and aggregates are separately heated in hot mixing plant to a temperature of 155-163 “C and 150-177 °C respectively.
Both are then mixed thoroughly to get a homogeneous mixture. For small work where hot mixing plants are not available, a hand-operated drum mixer is used.
Construction: The prepared sub-grade or sub-base is cleaned of dust and dirt by brushing, grooming, and dusting with sacks. A layer of bituminous binder is then applied on the sub-grade.
The mix of aggregates and binder is then spread by means of a self-propelled mechanical paver with suitable screeds capable of spreading, tamping, and finishing the mix. In small works spreading of Mx is also done manually.
The temperature of the mix at the time of spreading should be maintained in the range of 121-183C.
After spreading of the mix rolling is done by using 8 to 10 tones roller. The rolling is started from the edge and progresses towards the center. The rolling is continued until the entire surface is compacted.
Write a short note on:
A. Prime Coat
B. Tack Coat
C. Seal Coat
Prime Coat: A prime coat is an initial application of a low viscosity liquid bituminous material to an existing base of previous texture like W.B.M.
A low viscosity cutback is used as a bituminous primer. BIS has recommended the use of RC-0, MC-1, and SC-1 as primers.
The functions of prime coat are:
d. To seal the pores by penetrating into it.
e. To waterproof the underlining layer
f. To coat and bond dust and lose mineral particles
Tack Coat: It is an application of a bituminous binder to an existing surface to ensure a bond between the new construction and the old surface.
Road tar (RT-3), penetration grade bitumen (80/100), cutback sand emulsions are used as tack coats. As the surface on which it is applied are comparatively impervious, the quantity of binder required is less than the prime coat. Tack coat serves the same functions as the prime coat.
Seal Coat: It is a very thin surface treatment or a single coat of surface dressing applied on the existing black top surfacing. It is laid as a final coat over certain bituminous pavement which is not impervious. Penetration macadam, bitumen bound macadam, and premix carpet is open graded bituminous construction and requires the application of seal coat. It is also provided over existing bituminous pavement which is worn out.
Also, Check This.
- How to get construction license
- UNDERGROUND WATER TANK
- What are Different Tests for Concrete Quality Check