What is Pier? What is the function of Pier? What are the different shapes of Piers available?
Piers are structures located at the ends of bridge spans at intermediate points between the abutments. The function of piers is two-fold: to transfer the vertical loads to the foundation, and to resist all horizontal forces and transverse forces acting on the bridge.
Being one of the most visible components of a bridge, the piers contribute to the aesthetic appearance of the structure.
The general shape and features of a pier depend to a large extent on the type, size, and dimensions of the superstructure and also on the environment in which the pier is located. Piers can be solid, cellular, trestle, or hammerhead types (Fig. 3.2).
Solid and cellular piers for river bridges should be provided with semicircular cutwaters to facilitate streamlined flow and to reduce scour. Other designs such as reinforced concrete framed type as shown in Fig. 3.2 have also been used.
Solid piers can be of mass concrete or of masonry for heights up to about 6 m and span up to about 20 m.
It is permissible to use stone masonry for the exposed portions and to fill the interior with lean concrete.
This would save expenses on shuttering and would also enhance appearance. The stone layers should be properly bonded with the interior with bond stones.
Single column piers are increasingly used in urban elevated highway applications, and also for river crossings with a skew alignment. In an urban setting, single-column piers provide an open and free-flowing perception to the motorists using the road below.
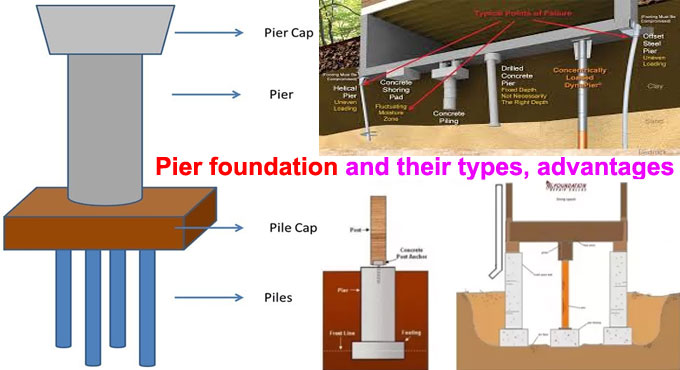
Such piers when used for a skew bridge across a river result in the least obstruction to the passage of flood below the bridge.
Cellular, trestle, hammerhead, and single-column types use reinforced concrete and are suitable for heights above 6 m and spans over 20 m.
The cellular type permits saving in the quantity of concrete, but usually requires difficult shuttering and additional labour in placing reinforcements.
The thickness of the walls should not be less than 300 mm. The lateral reinforcement of the walls should be more than 0.3 percent of the sectional area of the wall of the pier, and the quantity should be distributed as 60 percent on the outer face and 40 percent on the inner face.
The trestle type consists of columns (usually circular or octagonal) with a bent cap at the top, In some recent designs, concrete hinges have been introduced between the top of the column and the bent cap in order to avoid moment being transferred from deck to the columns.
For tall trestles, as in flyovers and elevated roads, connecting diaphragms between the columns may also be provided.
The hammerhead type provides a slender substructure and is normally suitable for elevated roadways. When used for a river bridge, e.g., Jawahar Setu across Sone river at Dehri”, this design leads to minimum restriction of the waterway.
The construction procedure should be arranged such that the construction joints are mìnimized, by adopting continuous concreting or by use of slip form technique to the extent possible. The simple geometry of the pier leads to reduced construction costs.
How the width & length of Pier is selected? Explain.
The top width of the pier depends on the size of the bearing plates on whích the superstructure rests.
It.is usually kept at a minimum of 600 mm more than the out-to-out dimension of the bearing plates, measured along the longitudinal axis of the superstructure. to-out dimension of the bearing plates measured perpendicular to the axis of the superstructure.
The bearing plates are so dimensioned that the bearing stress due to dead and live loads does not exceed 4.2 MPa.
When the length of a pier is narrower in plan than the width of the bridge deck carried so that the deck cantilevers beyond the pier edges, the pier is called an inboard pier.
Such piers are used in a multi-span urban interchange featuring a flyover and ground-level slip roads, wherein the adoption of inboard piers offers considerable saving in the use of costly urban land that would have been required when full-width piers are adopted.
In addition, inboard piers for urban interchanges facilitate improved sightlines for vehicles passing the piers and enhance the overall appearance.
Other innovative designs for piers to suit urban site requirements Include H-shaped piers flaring at the top, which provides a wider base at the top of the pier for the stability of the deck and limited use of space at the base of the pier at the ground level.
The bottom width of the pier is usually larger than the top width so as to restrict the net stresses within the permissible values.
It is normally sufficient to provide a batter of 1 in 25 on all sides for the portion of the pier between the bottom of the bed block and the top of the well or pile cap or foundation footing, as the case may be.
In the case of river bridges, the portion of the pier located ‘between wind and water’, that is, the portion of the masonry surface which lies between the extreme high and extremely low water is particularly vulnerable to deterioration and hence needs special attention.
This surface is subject to damage due to the impact of floating debris, the erosive action of the current, waves, and in the case of seawater or chemical environment to chemical
What are the various loads and forces to be considered in the design of Piers?
The load and forces to be considered in the design of piers are as below :
1. Dead load of the superstructure and the pier itself.
2. Live load of traffic passing over the bridge. The effect of eccentric loading due to the live load occurring on one span only should be considered.
3. Impact effect for the top 3 m of the pier only.
4. Buoyancy of submerged part of the substructure. If the pier is anchored to rock by dowels, it is permissible to neglect the effect of buoyancy.
5. Effect of wind on moving loads and on the superstructure.
6. Force due to water current
7. Force due to water action, if applicable.
8. Longitudinal force due to tractive effort of vehicles.
9. Longitudinal force due to braking of vehicles.
10. Longitudinal force due to resistance in bearings. In order to reduce the net longitudinal force in bearing, it is usual. to make bearings of two spans located on a pier to be of the same type, i.e., expansion bearings or fixed bearings. Still, a variation of about 10 percent in the frictional coefficients of the sliding bearing may be assumed. Also, the resistance in two adjacent bearings would differ when the live load occupies only one of the two adjacent spans.
11. Seismic effects
12. Force due to collision by barges for piers in navigable waters.
Difference between Pier and Abutment, full explanation in Hindi
Explain the effect of forces due to Wave Action and Collision in the case of Bridge Piers.
Forces due to Wave Action and Collision
There may be situations where the bridge pier is subjected to the action of waves, thereby experiencing additional hydrodynamic forces due to wave action.
A typical example is the Pamban bridge connecting the Rameswaram island with the Indian mainland. Also, if the bridge spans across a tidal river or an estuary, wave forces become significantly large.
The wave motion is essentially an unsteady fluid flow. The fluid particles are subjected not only to a velocity in the horizontal and vertical directions but also to accelerations in these directions.
Since the piers are normally rigidly fixed at the bottom, the horizontal forces only are of interest to the designer.
The fluid particle velocity and acceleration induce a horizontal drag force and an inertial force which taken together may be considerably large.
In the case of major bridges in waters, it is to for the possibility of boats, barges and with the during storms and foggy weather.
For example, Mandovi and Zuari bridges on National Highway No. 17 in Goa have to allow very heavy barge traffic in the rivers to transport iron ore for export.
Collision of the barges with the piers should be prevented to the extent possible, to avoid damage to both the bridge and the barge.
The best protection from the point of view of safety to the barge is a fender of wooden piles around the pier. However, such Wooden piles have not been effective in the case of Mandovi’s first bridge. Hence, more complicated concrete fenders were adopted for the Zuari bridge.
The determination of the magnitude and direction of the collision force to be provided for in the design is difficult, requiring considerable engineering judgment, and can best be done after conducting model tests and theoretical assessment of the probability of occurrence of a collision.
When barge impact is to be provided for, only solid type piers are to be adopted.
What is Abutment? What are the various components of it? Also, discuss the forces considered for its design.
An abutment is a substructure that supports one terminus of the superstructure of a bridge and, at the same time, laterally supports the embankment which serves as an approach to the bridge.
For a river bridge, the abutment also protects the embankment from Scour of the stream. Bridge abutments can bé made of masonry, plain concrete, or reinforced concrete.
An abutment generally consists of the following three distinct structural elements :
(i) the breast wall which directly supports the dead and live loads of the superstructure, and retains the filling of the embankment in its rear ;
(ii) the wind walls, which act as extensions of the breast wall in retaining the fill though not taking any loads from superstructure; and
(iii) the back wall (also known as dirt wall), which is a small retaining wall just behind the bridge seat, preventing the flow of material from the fill on to the bridge seat.
In abutment design, the forces to be considered are :
(1) Dead load due to superstructure.
(2) Live load on the superstructure.
(3) Self-weight of the abutment.
(4) Longitudinal forces due to tractive effort and braking and due to temperature variation and concrete shrinkage.
(5) Thrust on the abutment due to retained earth and effect of live loads on the fill at the rear of the abutment.
The latter effect is considered in design as an equivalent surcharge. The Bridge Code (Clause 714.4) requires all abutments to be designed for a live load surcharge of 1.2 m height of earth fill.
Of the above forces, the earth pressure is the most difficult to compute correctly. the magnitude of earth pressure varies with the character of the material used for backfill and the moisture content.
The earth pressure may be computed as indicated in Section 3.16.
It is important in abutment construction to place the fill material carefully and to arrange for Its proper drainage. A good drainage system may be secured by placing rock fill immediately behind the abutment.
The braking force is usually larger than the tractive effort and is taken as 0.2 of the weight of the design vehicle.
The other longitudinal forces due to temperature variation and concrete shrinkage at the bearing level may be conservatively assumed as 10% of the dead load from superstructure”.
State how the backfill behind an abutment is to be constructed.
Backfill behind Abutment
The design and construction of the backfill and drainage behind the abutment should be carefully attended to. A layer of filter material well packed to a thickness of 600 mm should be provided over the entire surface behind the abutment, with a smaller size towards the soil and a larger size towards the wall.
An adequate number of weep holes should be provided to prevent any accumulation of water and building up of hydrostatic pressure behind the walls.
The weep holes may be of 100 mm diameter with 1 in 20 slopes placed at about 1.0 m spacing in both directions above the low water level.
The backfill should be of clean broken stone, gravel, sand, or any other pervious material of adequate length to form a wedge of cohesionless backfill.
The fill should be compacted in layers. Cohesive backfill should be compacted in layers by rollers to the maximum dry density at optimum moisture content.
The sequence of filling behind the abutment should be controlled to conform to the assumptions made in the design.
For example, if the earth pressure in front of the abutment (normally ignored) has been assumed in design, the front filling should be done along with the filling behind the abutment layer by layer.
Similarly, if the design assumes that the dead load of the superstructure exists when the earth pressure due to embankment is applied, the filling behind the should be deferred till the placement of the superstructure.
What are the different types of foundations used in Bridge Structures?
The foundations used in bridge structures may be broadly classified as :
(i) Shallow foundations, and
(ii) Deep foundations.
A shallow foundation is sometimes defined as one whose depth is smaller than its width. For the purpose of discussion in this chapter, a shallow foundation is taken as one which can be prepared by open excavation, and a deep foundation would refer to one which cannot be prepared by open excavation.
Footings and raft foundations are examples of shallow foundations. Shallow foundations transfer the load to the ground by bearing at the bottom of the foundation. In the case of a deep foundation, the load transfer is partly by point bearing at the bottom of the foundation and partly by skin friction with the soil around the foundation along its embedment in the soil.
Deep foundations are further classified as :
(a) Pile foundations, and
(b) Caisson foundations.
A pile is defined as a column-support type of foundation which may be precast or formed at the site. Caisson (well) foundation is a structure with a hollow portion, which is generally built-in parts and sunk through the ground to the prescribed depth and which subsequently becomes an integral part of the permanent foundation.
Caisson foundations are of two types :
(c) Open caissons (also known as well foundations in India); and
(d) Pneumatic caissons.
An open caisson is one that has no top or bottom cover during its sinking. It is more popularly known as well foundation. A pneumatic caisson is a caisson with a permanent or temporary roof near the bottom so arranged that men can work in the compressed air trapped under it.
Pneumatic caisson can be used for a depth of about 30m below water level, beyond which pile foundations would have to be resorted to.
The selection of the foundation system for a particular site depends on many considerations including the nature of the subsoil, the presence or otherwise in the subsoil of boulders buried tree trunks, etc., and the availability of expertise and equipment with the contractor operating in the region where the bridgework is located.
Constructibility is of primary importance in selecting the method of construction and deciding on the details of the foundation components. This is particularly important for over-water bridge piers. Generally. piles would be suitable when a thick stratum of soit sol overlays a hard soil. Caissons are preferred in sandy soils.
It is not uncommon to come across cases where a contractor owning pile driving machinery, would quote lower for precast pilling, even when the client has specified open caissons.
Also, Read this