Contractor agreement construction activities is a legal document which acts as a legal binding between both the parties, For all the terms and conditions mentioned in the said document, Construction activities take a considerable time to complete and involve many agencies.
- Legal conditions
- Responsibilities of contractor
- Scope of work
- Payment terms
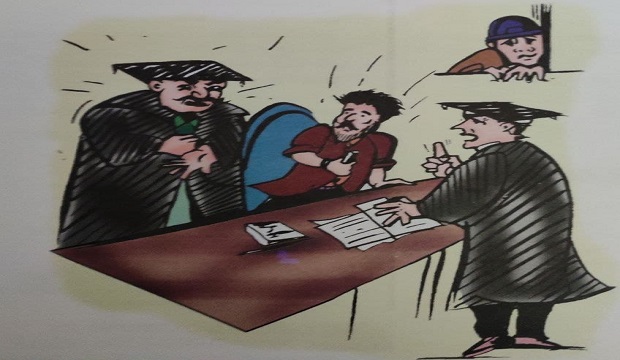
ADVANTAGES OF AN CONTRACTOR AGREEMENT
- Confirms the rates of various items.
- Provides legal binding & support to both the parties in case of disputes, arbitration. sudden mishap etc.
- The contractor gets an idea about the scope of work, other conditions, and mode of measurement before commencing the work.
- The contractor understands the work procedure and the quality expected.
- The agreement helps reach understanding between both parties before the work begins. This minimizes the chances of a dispute that may arise without an agreement.
- The contractor can make budgetary provisions as per the payment terms in the agreement.
- He can estimate the total expenses, overheads for the requirement, specification, quality of work, etc. for each item.
FORMALITIES REQUIRED FOR THE CONTRACT OR AGREEMENT
- Name of the owner and address
- Name of contractor’s firm and address
- Stamp paper of appropriate value
- Type of the work and address
- Type of work and building name
- Approximate cost of the work to be executed under agreement
- Approved quotation from a contractual agreement for all construction activities
- Detailed specifications of the work
- Working drawing set
- Drawings and sketches about typical work systems
Verification of the contractor should be done for
- The capacity of executing the work
- Inspection of earlier work done by him
- Machineries available with him
- Manpower and complete setup
- Quantity and quality of material available
- Financial status
- Experience of similar work
- Present quantum of work in hand
- All supporting documents for firm registration, license, insurance, income tax clearance, etc.
BASIC ROLE AND RESPONSIBILITIES OF CONTRACTOR
The basic responsibilities contractor will be the same, for all types of construction work activities. The following points should be considered in the agreement in detail
- Progress of work
- Quality of work
- Speed of work
- Rejection of work
- Defects, improper work and substandard
- materials
- Lead of material
- Additions and alterations
- Temporary labour hutments
- Supervision of work
- Salary and wages of labour
- Subletting
- Damages done
- Termination of contract
- Payments terms
- Advance payment
- Retention amount
- Final bill
- Arbitration
CONTRACTOR AGREEMENT FOR ALL CONSTRUCTION ACTIVITIES – LABOUR
- Agreement with any contractor depends on the terms and conditions mutually decided between the labour contractor and builder/owner.
- In this chapter, the basic guidelines for preparing agreements for any work are discussed.
- The conditions for each work are considered while preparing an agreement.
- But they may vary as per the type of contract, type of work, place of work. stage of work etc.
1. AGREEMENT WITH R.C.C. CONTRACTOR
Normally, R.C.C. work can be given to the labour contractor on a built-up area basis, which is very easy for calculation of payments, settlements, etc.
SCOPE OF WORK
- The scope of the labour contractor’s work includes all R.C.C. work connected with the building such as footings, columns, beams, slabs, lintels, pardies, staircases, lofts, chajjas, R.C.C. elevation features.
- suction tank, overhead water tank, machine rooms. parapets etc. R.C.C. works connected with the building and all works up to the plinth level such as excavation in all kinds of soils up to the strata as instructed and desired by the R.C.C.
- Consultants. removal of excavated materials, backfilling, plinth filling soling, P.C.C. brick Block U.C.R. masonry in the plinth, etc.
SUPERVISION
A full-time supervisor/engineer should be engaged by the labour contractor to supervise all the work.
All the major concreting shall be machine-mixed and all required machineries should be brought by the contractor. He will be responsible for its maintenance and supply of fuel.MACHINERY
SHUTTERING
For the works of footings., columns, beams, slabs, lofts, chajjas parties, and all other R.C.C. works shuttering shall be provided by the Labour Contractor including the required quantity of nails and binding wire.
Shuttering should be of the approved and standard quality as decided by the builder/owner.
OILING
All planks. plyboards. steel centring plates shall be applied with de-shuttering oil, as approved by the engineer, before reinforcement. The black oil or waste motor oil shall not be used.
BINDING WIRE
Binding wire for holding the formwork centring in position shall be provided by the Labour Contractor at his cost.
STEEL REINFORCEMENT
The Labour Contractor is responsible for the proper utilization of the steel lot supplied to him. Bars shall be cut, bent, hooked and placed in position as per schedule/detailed R.C.C. drawings or as chairs, cover blocks, as required directed. shall be provided by the labour contractor agreement for all construction activities.
HONEYCOMBING
All R.C.C. surfaces shall be absolutely vertical/ horizontal with a perfect, of honeycombing, it shall be cleaned with a wire brush, water and repaired by the contractor at his cost.
DE-SHUTTERING
For all R.C.C. work, the de-shuttering period will be as specified by the structural consultant.
CURING
All R.C.C. works shall be adequately and sufficiently cured by the Labour contractor agreement for all construction activities.
B.B. MASONRY UP TO PLINTH
All burnt brick masonry up to the plinth level shall be done by the Labour Contractor. He shall also complete the necessary plinth filling soling, P.C.C, etc. up to the plinth level.
RAILING
The labour contractor shall provide a wooden plank railing at his cost. It should be fixed firmly on bullies @ 2.4 m (8) c/c embedded in concrete and at 1.5 m (5) distance all around the building, The planks shall be 15 cm (6″) wide and shall be in one line and level, with right angles at corners.
HACKING
All R.C.C. works shall be hacked with Tacha by the Labour The contractor at his cost, while the concrete is green. It is understood that the hacking shall be at least 500 notches per sq.m. (50 os./s.ft.) of surface area.
GRID LINES
The grid lines should be marked on plinth P.C.C. and on every slab for proper line out of columns above the plinth/slab level by the Labour Contractor at his cost.
JOINING AT EXPANSION JOINT
The Labour Contractor shall fix the pre-molded bituminous sheet and/or any expansion joint materials supplied by the builder’s owners for expansion joint in the R.C.C. works at his cost.
DOWEL BARS
The dowel bars for steel reinforcement are required to be provided at any junction for future work. They shall be provided by the Labour The contractor as part of the steel reinforcement works.
COVER BLOCKS
For all R.C.C works, the cover blocks for covers, as specified by the consultants, shall have to be made by the Labour Contractor and fixed in all R.C.C. work. Material for making cover blocks shall be supplied by the Builders owners.
SCAFFOLDING
Scaffolding for all R.C.C. works, hoist and lift shall be done and dismantled by the Labour Contractor. along with the material, at his cost.
SPACE FOR MACHINERY
Space for mixer or lift shall be cleared by the Labour contractor at his cost.
EMPTY CEMENT BAGS
The labour contractor shall return all empty bags of cement to the storekeeper before demanding further cement for any work for that/next day’s work.
MODE OF MEASUREMENT OF R.C.C. WORK
- The built-up area will include all passages, balconies, staircase, parking and flat areas, All open spaces such as staircase voids. ducts etc. shall not be included in the built-up area.
- The overhead water tank area shall be included in the built-up area as one slab area.
- The parking area shall be considered for R.C.C. work.
SCHEDULE OF RATE R.C.C WORK
- The labour rates for all R.C.C. works of the building is submitted by the labour contractor agreement for all construction activities.
- The builder/owner negotiates the rates and acceptance rates are agreed by both (contractor and owner).
- The net rate for R.C.C. work, mentioned in the agreement can be on the built-up area say Rs. XYZ per sq.m./s.ft.
- If the work is given on an item rate basis, the rates for all the R.C.C. items can be decided separately with convenient units.
MODE OF PAYMENT R.C.C WORK
(a) IF THE WORK IS ON BUILT-UP AREA BASIS
Payment can be made to the contractor on the basis of the work progress.
The progress of work is divided into different work stages as a percentage, Basically, this percentage break-up can be calculated as per the quantum of work involved, at that particular stage.
Specimen percentage breakup for the typical building of ground + 3 floors is shown in the table.
MOD OF PAYMENTS – REINFORCEMENT CEMENT CONCRETE
SR NO
|
ITEM
|
PERCENTAGE
|
1
|
Plinth
|
14%
|
2
|
First slab
|
14%
|
3
|
Second slab
|
15%
|
4
|
Third slab
|
15%
|
5
|
Fourth slab
|
17%
|
6
|
O.H.W.T. + Staircase cap
|
10%
|
7
|
Loft/lintel/chajja/staircase pardi
|
10%
|
8
|
Elevational features
|
5%
|
Total
|
100%
|
(b) IF THE WORK IS ON ITEM RATE BASIS
Payment can be made as per the bill, prepared according to the actual joint measurement of work done at the site and the respective rate of that item.
2. AGREEMENT FOR MASONRY AND PLASTER WORK
The labour work contract for masonry and plastering work can be given on a built-up area basis. Bills for any stage of work can be prepared quickly and very conveniently when the built-up area calculations are done.
SCOPE OF WORK
The scope of labour contractor’s work includes the masonry and plaster works for the buildings, as per drawing details and specifications, shown in the architects near me working drawing.
SUPERVISION
A full time experienced supervisor/engineer shall be engaged by the labour contractor to supervise all the work.
LINE-OUT (PERANI)
Before starting the masonry work, the labour contractor will lay only one layer of brick and/or block called Rangat’ or ‘Perani’ for the entire floor.
WET BRICKS BLOCKS
Dry bricks/blocks shall not be used. contractor shall ensure that the bricks are soaked The labour in water before use.
MORTAR-JOINT
- It is clearly understood that no mortar joint shall exceed 15mm (1/2”).
- The surface of each course shall be thoroughly cleaned before laying the next course.
HORIZONTAL R.C.C. BAND
“The labour contractor shall provide a horizontal band with reinforcement as required in brick/block masonry.
CURING
All masonry and plasterwork shall be adequately and sufficiently cured by the labour contractor, at no extra cost.
The minimum curing period shall be as follows
- All types of masonry work = 14 days.
- All external plasterwork = 21 days.
- All internal plasterwork = 14 days.
For Internal plaster -> Curing for the first 3 days should be done using a bucket and tin only. Do not use hose pipes. The finishing of sanla Neeru plaster may be damaged due to pressure.
FIXING OF DOOR AND WINDOW FRAMES
The labour contractor shall ensure that the frames are fixed in the proper plumb, level and line and the holdfasts are to fixed (6 No. for doors & 4 No. for windows) properly in the adjoining masonry and/or R.C.C. columns.
FIXING OF ALUMINIUM FRAME
For the fixing aluminium windows, the labour contractor shall provide the required opening with the template (farma), to get accuracy in line, level, plumb, and right angle.
BALCONY WATER SPOUTS
The labour contractor should fix, water spouts properly in a corner away from the balcony door, before plastering the balcony.
SCAFFOLDING
Scaffolding material for all the masonry and plaster works shall be brought, erected and dismantled by the labour contractor agreement for all construction activities.
CHICKEN MESH FIXING
The labour contractor shall fix the chicken mesh in the joint of R.C.C. and masonry. The chicken mesh shall be provided by the builders/owners.
NIGHT WORKING
If the labour contractor needs to work at night, he should arrange for the electric wire and bulb/tube light fittings at his cost.
TOOLS & TACKLES
The labour contractor should buy good quality tools & tackles for masonry & plasterwork, like a sand sieve, ghamela, phawada, tikav, hammer, aluminium Patti, randha, thapi, sponge, level tube, line Dori, etc.
LEAD OF MATERIAL
No extra charges should be paid for the horizontal lead up to 45 m (150′) for any material.
BUTT FILLING
The labour contractor should complete the butt jad finishing of all mosaic skirting, glazed tiles dado, kitchen platform, cuddappa shelves, ghabadi, etc. at no extra cost.
SCHEDULE OF RATE
If masonry and plasterwork are on an item rate basis, the rate for each item of work shall be mentioned in the schedule of rate. for a convenient unit of work.
If masonry and plaster are on a built-up area basis, the total rate for all works, as mentioned in the agreement, will be Rs. XYZ per sq.m. (or per s.ft.)
MODE OF MEASUREMENT PLASTER WORK
(a) IF THE WORK IS ON ITEM RATE BAS’S
Follow the mode of measurement as per the standard rules in I.S. Code i.e. For door and window frame full deduction in masonry and half deduction in plaster from both sides.
No separate measurements for an edge. corners, jams, etc.
(b) IF THE WORK IS ON BUILT-UP AREA BASIS
All areas will be the same as the R.C.C. area except for parking. Considered 50% area only for parking.
MODE OF PAYMENT PLASTER WORK
(A) IF THE WORK IS ON ITEM RATE BASIS
Direct measurement shall be taken at the site for the actual work done and payment shall be made accordingly.
(B) IF THE WORK IS ON BUILT-UP AREA BASIS
The following guidelines are given to split up the. percentage of the amount of work done, considering the quantum of work involved in each item.
SR NO
|
ITEM
|
PERCENTAGE AMOUNT
|
1
|
MASONRY INCLUDING
DOOR FRAME AND
MS WINDOWS FIXING
|
36%
|
2
|
EXTERNAL SAND FACE PLASTER
|
30%
|
3
|
INTERNAL NERU PLASTER
|
28%
|
4
|
BUTT/JAD FINISHING
|
4%
|
5
|
GABHADI WORK/TOUCH
UP WORK
|
2%
|
TOTAL
|
100%
|
3. AGREEMENT WITH TILING CONTRACTOR
- Tiling work is generally on an item rate basis since there might be considerable changes in the types, of flooring and dado.
- Measurement of tiling work is not difficult, hence practice on a built-up area basis can be done if the detail specifications are ready in advance.
- The following points should be considered while preparing agreements with the tiling contractor to act as a guideline and the work procedure should be written in detail and supplemented by working sketches.
CLEANING
The labour contractor should ensure that the base slab is cleared of all loose mortar/other materials and is finished to a reasonably true plain surface.
SORTING OF TILES
The labour contractor should lay the separate batches of tiles supplied by the manufacturer, in separate areas. He will be responsible. for any variations in shades due to the mixing of two lots.
LEAD AND LIFT
The labour contractor should carry and lift the lime mortar or sand and instant lime to the actual place of work at his own cost, up to a lead of 45 m (150).
TOOLS MACHINERIES
The labour contractor should provide all tools and machineries required for the work.
MIXING
The labour contractor should take proper care to keep the required amount of water in the lime mortar to avoid the formation of any hard lumps in the mortar.
WASTAGE
He should see to it that the wastage does not exceed 2%. If it exceeds 2%, the cost of the extra wastage shall be deducted from his running bills.
LAYING TILES
The labour contractor should start fixing of the tiles from the top floor and work downwards or from the innermost room to the exterior of the flat/ unit, unless otherwise directed by the site in-charge.
SLOPES
The labour contractor should fix the tiles with the required slopes.
TILES CUTTING
Wherever the tiles are required to be cut before placing, they should be cut be machine-cut. Under no circumstances should they be cut by hand.
JOINT FILLING
After fixing the tiles on true surfaces and levels as detailed above, they should be allowed to be set overnight.
The contractor should ensure that the joints are cleaned with a wire brush and thin blade and carry out the grouting right through the joint up to the bedding mortar.
CURING
The labour contractor shall carry out the curing as per the given table at his own cost.
SKIRTING STEPS AND RISERS
- The contractor should not be allowed to chisel the columns. For this, he should use the 12 mm (“) thick skirting tile.
- The labour contractor will ensure that the riser and steps are equal and the nosing line is straight.
- He shall lay the skirting to a uniform line and level projecting 8 mm beyond the wall plaster surface with the help of wooden farma.
POLISHING
- The labour contractor should start the polishing work 14 days after the curing of the flooring with the appropriate quality of polishing stones. first grinding shall be fully done and if any joints are found to have opened out, they shall be cleaned from the grinding slurry and refilled properly and thoroughly.
- This shall be cured by the labour contractor for a minimum of four days, at no extra cost.
- The labour contractor should carry out the cement grouting of tiles immediately after completing and cleansing of the first coat.
- The second coat should be given after four days of curing, for freshly grouted areas.
- The labour contractor will carry out one or more polishing coats until the desired level of finishing is attained.
- The final grinding coat of oxalic acid should be carried out as directed by the site in charge. The labour contractor shall provide the required quantity of acid at no extra cost.
DEFECTS IN WORK
The labour contractor will also attend to any defects. that are noticed during the progress of works or even at the final completion stage, for which no extra charges should be demanded/paid.
ACID WASHING
The labour contractor should check that all the glazed/ceramic tile work is washed with acid, as directed by the site in charge. The required quantity of acid for this purpose should be. by him at his own costs.
KITCHEN OTTA
- The labour contractor should provide holes in cuddappa stones for fixing the gas cylinder connections as well as in the sink for fixing the outlet pipe. No extra charges should be paid for this.
- After the completion of platform erection work, the labour. the contractor should complete all ghabadi work in the plaster made for the erection of the platform.

- During the process of fixing and polishing, the following mistakes should be avoided.
- Walking on the floor with muddy feet/dirty shoes.
- Work of wooden furniture/polishing of wooden doors without taking enough precautions.
Mode of Payment – tiling
STAGES OF THE WORK
|
PERCENTAGE AMOUNT PAYMENT
|
ON COMPLETION OF FIXING TILES
|
50%
|
ON COMPLETION OF FIRST COAT + GROUTING
|
25%
|
ON COMPLETION OF SECOND COAT
|
10%
|
ON COMPLETION OF THIRD COAT
|
05%
|
ON COMPLETION OF FOURTH COAT + ACID
WASHING + CLEANING AND RECTIFICATION
CLEANING FROM SITE ENGINEER COUNTER
SIGNED BY P.M
|
10%
|
100%
|
GLAZED / SPARTEX / CERAMIC / MRUDUL/ SHIN TILING
STAGES OF THE WORK
|
PERCENTAGE AMOUNT PAYMENT
|
ON COMPLETION FIXING
|
85%
|
ON COMPLETION OF THE FIRST COAT OF ACID
CLEANING
|
7.5%
|
ON COMPLETION OF THE SECOND COAT OF
ACID+ CLEANING/JATT FIXING ETC. ON
FLOORING TEST FOR WATER LEAKAGE
|
7.5%
|
100%
|
KITCHEN OTTA CUDDAPPA
STAGES OF THE WORK
|
PERCENTAGE AMOUNT PAYMENT
|
ON COMPLETION OF FIXING
KITCHEN PLATFORM, FACE PATTI,
AND SINK
|
85%
|
ON COMPLETION OF POLISHING OFF
CUDDAPPA PLATFORM AND FACE
|
10%
|
ON FINAL CLEANING RECTIFICATION
COMPLETION OF GABHADI AND
SUBMISSION OF FINAL BILL WITH CLEARANCE
FROM SITE ENGINEER
|
05%
|
100%
|
4. AGREEMENT FOR WATERPROOFING WORK
Water-proofing work can be given on an item rate basis, instead of on an area basis. Here, the procedure sequence and other related works are important. While preparing the water-proofing agreement, the following points should be considered.
SURFACE PREPARATION
The labour contractor should ensure that all the necessary chasing of plastering, cleaning, etc. is completed before starting the water-proofing work.
PROCEDURE OF WORK
The labour contractor should follow the procedural Instructions of the site in charge of work at all stages.
SOCKETING AND CEMENT GROUTING.
The tabour contractor should ensure that there is no leakage of water in the socketing and cement grouting. before starting the first coat.
BASE COAT
The labour contractor shall provide a 25 mm to 40 mm thick cement mortar base coat.
WATER ESCAPE PIPE
The labour contractor shall provide a 25 m diameter G.J. pipe outlet for water escape. just above the base coat in all W.Ca.., Baths & toilets at no extra cost.
BRICK BAT COBA
The labour contractor shall carry out brickbat Coba by selecting well-burnt brickbats, soaked in water and joints filled with cement mortar of 1:4 proportion, and using the appropriate water-proofing compound.
FINAL TOPPING COAT
The labour contractor shall carry out the topping coat with 1:4 cement mortar mixed with the water-proofing compound.
CURING
Curing of all coats should be done by labour contractor for the minimum required period.
KITCHEN SINK OUTLET AND PASSAGE DROPS
The labour contractor should carry out the water-proofing in this case as per the procedure listed above.
TOOLS AND EQUIPMENT
The labour contractor shall provide the equipment, sockets, ladders for overhead water tank water-proofing, etc.
SAND SCREENING AND WASHING
The labour contractor will screen and wash the sand for his work, by employing his own labour and cost.
TERRACE WATERPROOFING
The labour contractor shall carry out the work as per the instructions of the engineer. The following are the steps involved in the work.
- Water-proofing of overhead water tank from inside and top.
- Employing the box type method for underground water tank, lift pit, basements, etc.
TEN YEARS GUARANTEE
The labour contractor shall submit a guarantee of ten years for the work, in the format supplied by the builder. During this period, the contractor will rectify the defects, if any, at his own cost.
MAINTENANCE OF THE WORK
The labour contractor must agree to the maintenance of the water-proofing work for a period of ten years, from the date of completion of the work.
MODE OF MEASUREMENTS WATERPROOFING WORK
- The surface area will be measured in s.ft.
- The water-proof area on the sidewalls for baths, toilets, and W.Cs below the finished level of topping coat shall NOT be measured in s.ft.
- Side watts coping of the terrace shall be measured in r.ft.
5. AGREEMENT WITH PLUMBING CONTRACTOR
The labour work for plumbing and sanitation can be given on an items rate basis. The agreement for the work can be prepared with the following points as a guideline. Also, the procedure should be written in detail with working sketches.
SCOPE OF WORK
The builders shall provide all the materials required for plumbing and sanitation works. The labour contractor shall maintain an account of the materials handed over to him.
MANPOWER & TOOLS
The labour contractor shall provide manpower and machinery with all necessary tools and accessories.
INSTRUCTIONS FOR WORK
The labour contractor shall carry out the works as per the instructions of the Project Engineer.
LICENSE FOR WORK
The labour contractor shall have to work under a licensed plumber and all Municipal Corporation/ Government correspondence shall be made under his license.
CUTTING, THREADING COST
All cutting of C.I./G.I pípes, threading of G.L pipes, if required, shall be done by the labour contractor without any extra charges.
LEAD JOINTS
The labour contractor shall carry out all the required lead joints and caulking and testing as per the standard procedure.
COAL TAR HESSIAN CLOTH
Labour contractors should not use any G.I. pipes in concealed piping without applying two coats of coal tar and Hessian cloth.
LINE OUT
All the internal and external piping work will be done after proper line-out on the walls, as per the drawings and approval for the same are obtained from the Project Engineer.
FINISHING
The labour contractor shall ensure that the finish of all the surface holes, gabhadi, etc. matches the finishing of the existing wall surface.
SCAFFOLDING
The labour contractor shall provide the scaffolding material required. Erecting and dismantling of the scaffolding will also be done by him.
LEAD
The labour contractor shall collect all the required materials from the store at the site, irrespective of any lead.
EXTERNAL PLUMBING
The labour contractor shall fix all the external C.I./ P.V.C. lines/as specified by the consultant.
INTERNAL PLUMBING CLEANING
The labour contractor shall carry out the chasing work for internal concealed G.I. piping and fixing of concealed G.I. pipes before water-proofing work.
TESTING
After the water-proofing work is over, the labour contractor shall test all concealed G.I. pipework with a pressure pump at the specified pressure.
LEAKAGE RECTIFICATION
If any leakage is noticed, the labour contractor should rectify the same at his cost.
STRUCTURAL STABILITY
The labour contractor should not puncture any R.C.C. member under any circumstances.
RATES
All the rates agreed in the schedule are inclusive of making openings and finishing the same after necessary C.I./ G.I. piping work in the best manner as per the adjoining plaster.
CURING
All the joints in C.I. piping and ghabadi work should be cured for at least seven days by the labour contractor at no extra cost.
RETENTION
It is agreed that 10% of the bill amount of the C.I./ G.I. pipeline work (apart from the retention amount) shall be retained until testing and shall be returned in the running bill, as soon as satisfactory testing is completed.
STANDARD HEIGHTS OF FITTINGS
The various fittings in sanitary and plumbing work should be provided at the heights mentioned in the drawings, given by the plumbing consultant.
AUTHORITY SPECIFICATION
All work carried out by the labour contractor should adhere to the specifications, rules and regulations of the local authority/Government.
DAMAGES
The builders reserve the right to debit the labour contractor for the cost of any material damaged while handling/working and necessary rectification of any completed work.
SUPERVISION
The labour contractor should carry out the work under his personal supervision and should remain present on-site, during the execution of the work.
MAINTENANCE OF WORK
The labour contractor shall carry out the maintenance work of common areas and each flat/office/ shop. free at of cost during the construction period.
HOLES IN MASONRY R.C.C.
Labour the contractor should carry out all necessary repairs to the holes in masonry, required to run the C.I./P.V.C. lines.
ESTIMATION
Plumbing the contractor should give the estimated quantities required for a particular work and he shall be held responsible for any excess or less, materials at the site.
MODE OF MEASUREMENT
The mode of measurement will be as per the IS codes.
REFINISHING WORK
The cement and sand for the refinishing work shall be provided by the builders, free of cost, to the electrical contractor.
CERTIFICATION OF BILLS
All the bills prepared by the electrical contractor shall be certified by the concerned Project Engineer, before submitting it to the builders.
TESTING OF WORKS
If the material is found defective or it does not conform to the rules and regulations of the Electrical Board, they will be rectified by the electrical contractor at his own risk/cost.
RETENTION AMOUNT
The contractor should agree to the deductions made towards retention and T.D.S.
TEMPORARY AND PERMANENT CONNECTIONS.
The electrical contractor is fully responsible for the procurement of temporary as well as permanent electrical connections required for the building.
ELECTRICAL POINTS
The electrical contractor should ensure that the position of the light/plug point and switch/distribution boards are fixed as per the Architect’s drawings.
CONDUITS IN SLABS
The electrical contractor should employ a senior electrician during the conducting work and concreting of the floor slab, for supervision.
CHASING
The chasing for concealed conduits should be in straight alignment. It should be preferably machine cut.
BATTENS
In the case of open C.T.S. wiring, the electrical contractor should take due care to fix the battens truly vertical and horizontal, and in perfect right angle turnings. A coat of varnish should be applied to the battens before fixing them.
BOARDS AND BOXES
The electrical contractor should ensure that the switches/point boxes are fixed truly vertical.
M.C.B
The electrical Contractor should fix the M.C.B. in every unit at a convenient place e.g. passage.
METER CABINET WIRING
The electrical contractor shall see to it that the wiring in the meter cabin or the cabinet is carried out properly, with due allowance for loops.
SUPPLY CABLES
The electrical contractor should provide a separate supply cable for the lift room.
MAINTENANCE
The electrical contractor is responsible for the maintenance work of common areas & each flat/ unit, free of cost, during the construction period.
CO-ORDINATION AMONGST OTHER AGENCIES
The contractor should depute one experienced electrical engineer/supervisor who will be available at the site during work hours. He will facilitate the coordination of all the concerned agencies, until the completion of the entire project.
SPECIFICATION OF MATERIALS
Before commencing the work, samples of all materials to be used should be shown to the builders for approval.
MODE OF PAYMENT – ELECTRICAL WORK
STAGE OF THE WORK
|
PERCENTAGE AMOUNT PAYMENT
|
ON COMPLETION OF LAYING ALL
PVC PIPES IN SLAB AND WALLS
|
15%
|
ON SUPPLYING AND FIXING OF
MAIN WIRING AND BOARDS
|
30%
|
ON FIXING OF SWITCHES, BOX AND
OTHER ACCESSORIES
|
35%
|
ON COMPLETION OF TESTED ENERGY
METER FIXING & GETTING NOC FROM
THE SITE IN-CHARGE
|
10%
|
IN THE FINAL BILL AFTER SIX MONTHS
SATISFACTORY PERFORMANCE OF ALL
THE SYSTEM & APPLICATION
|
10%
|
100%
|
6. AGREEMENT WITH CARPENTRY CONTRACTOR
The following points should act as a guideline while drawing an agreement with the carpentry contractor.
SCOPE OF WORK
The labour contractor will provide men and machinery, as required, to carry out the carpentry work.
TOOLS MACHINERY
The necessary manpower, tools, machinery, etc. for the carpentry work, will be provided by the labour contractor.
LINE, LEVEL, PLUMB CHECKING
Labour the contractor should check that all door frames are truly vertical, before starting the door shutter fixing. If some of the door frames are not in plumb, they should be rectified by the labour contractor, free of cost.
WORK PLACE
All the carpentry operations such as sewing, cutting, etc. should be carried out at a fixed place & at the end of the day’s work, this place should be cleaned thoroughly.
ISSUE OF HARDWARE MATERIALS FITTINGS
All hardware materials, door fittings, etc. shall be issued as per the day’s consumption. The balance material, at the end of work, should be immediately returned by the labour contractor.
CHECKING OF THE HARDWARE ITEMS.
While fixing the door shutters, all hardware items should be checked by the labour contractor for quality, size, etc.
COVER MOULDINGS
The cover mouldings should be prepared as per the drawings given and should be fixed by the labour contractor free of cost.
MEASUREMENTS
The labour contractor should check all the window frames for their verticality and diagonals before they are fixed.
WASTAGE
Labour the contractor should ensure that there shall be minimum wastage in all materials during handling, cutting, etc. Care should be taken while fixing the fittings and hardware.
FIXING
All fittings should be fixed with screws only. Nailing should be strictly avoided. Drilling machines should be used for drilling holes. Direct hammering should be avoided.
COMPLETION
Fixing of the door shutter will be considered as incomplete even if a small work is kept pending. e.g. If all the screws are not fitted to the hinges, the work is incomplete.
MAINTENANCE
The labour the contractor should keep all the door shutters locked, as far as possible, This helps reduce the maintenance of the shutters in the Initial stages., Any requirements of maintenance shall be met by the labour contractor, free of cost.
SCHEDULE OF RATES AND PAYMENTS
The Schedule of rates and payments should be decided mutually by the labour contractor.
MODE OF MEASUREMENT CARPENTRY
- The mode of measurement can be decided mutually by the labour contractor. The following points can act as a guideline.
- On per number basis: No, of shutters with fixing of ready-made shutters, along with decided fittings, cover mouldings, etc., for main door/internal door/bath/W.C. door. balcony door.
- On sq.m./s.ft, basis: Shutter fixing on sq.m./s.ft. basis.
- Cover moulding: On r.ft. basis with making and fixing or only fixing.
- Door fittings: Per No. basis or per door basis.
7. AGREEMENT WITH THE TV TELEPHONE WORKS CONTRACTOR
TV/Telephone points should be provided in modern flats/bungalows. A separate agency can be engaged in such facilities.
SCOPE OF WORK
Includes the required cabling, from the central video room to individual building entrances, and from here to individual flats.
MATERIAL AND MANPOWER
The contractor should provide cable, wires, and other necessary fixtures for the work, as per the specifications.
SUPERVISION
The contractor should appoint an experienced supervisor to supervise the vertical conducting work in buildings and the main conducting work from the video room to different buildings.
TRANSPORT
All the wires, cables, fixtures, amplifiers, etc. should be brought at the site by the contractor at his own cost.
CABLING WORK
All necessary precautions should be taken during cabling work to avoid sharp turns and bends.
TESTING
After the total completion of the work, the contractor should test the facilities using a TV set and VCR in all the flats, free of cost.
AFTER N.O.C.
After necessary testings, the contractor should collect N.O.C. for work completed, from the site engineer.
MAINTENANCE
The labour the contractor should maintain the complete system, for a period of twelve months after the date of completion of work, free of cost.
MODE OF MEASUREMENT
The mode of measurement shall be decided on per flat basis for providing and fixing the complete system as per the specified materials, terms, and conditions.
MATERIAL SPECIFICATIONS
All electrical equipment/ accessories will be as per the specifications agreed with the client.
Cable and wires for C.A/TN. will be of the approved brand.
SCHEDULE OF RATES
As decided mutually with the contractor.
8. AGREEMENTS WITH THE PAINTING CONTRACTOR
- Generally, painting work can be given with material and labour contract, on an item rate basis.
- The following points should act as a guideline while preparing the agreement with the painting contractor.
- A detailed procedure of the painting work should be mentioned in the agreement, along with the required sketches.
SCOPE OF WORKS
The labour contractor shall complete all the painting work involved in the project as per the specifications and procedures approved by the engineer in charge.
- Donga application
- Surface preparation
- Putty application
- Primer application
- Various mix preparation
- Oil painting
- Distemper
- Cement paint
QUALITY OF MATERIAL AND BRUSH
The labour the contractor should use painting brushes and other materials of the specified quality.
PERMISSION
- The labour the contractor must obtain written permission from the site in charge, for each coat, before applying the next coat.
- Such approval should be attached to each R.A. bill of the labour contractor.
MAINTENANCE OF WORK
Painting the contractor should provide free maintenance, for a period of one year from the completion of the project.
TASK WORK OF LABOUR
The labour contractor shall not exceed the following work turn out limits i.e. the capacity of doing work by skilled labour in the form of quantity of work per day.
SCHEDULE OF RATES
Schedule of rates for 100% completion of each item m s.ft. rate basis can be decided mutually.
MODE OF PAYMENT
Decide the mode of payment mutually and mention it in the agreement, Refer to the following, split up in percentages, for various items during each stage of work as a guideline.
WHITEWASH DISTEMPER
10% on completion of scraping, cleaning, primer, putty, etc.
MODE OF MEASUREMENT
- The mode of measurement shall be as per IS 120O
- In the case of rolling shutters, no separate measurement shall be given for cover.
9. AGREEMENT WITH ROAD CONTRACTOR
The road work can be given on a material and labour contract basis, either directly on s.ft. basis för 100% work completion or on an item rate basis. The following points should be considered while preparing an agreement with the road contractor as a guideline.
SCOPE OF WORK
provide men, material, and machinèry. To give total finished road work, including semi-grout and complete asphalting with carpet and seal coat finish, etc.
MACHINERIES
The road the contractor should have the following machineries. No extra charges will be given for hiring any machineries. The typical machines used for the work are hot mixers. road rollers, water tankers, trucks, tempo for carting, hand carts, and other tools, bouser, etc.
DRAWING DETAILS
The labour the contractor should be able to read the drawings given to him and also necessary slope to the roads in cross-section and in L sections as shown in the drawings.
WORK STAGES
Total road work including semi-grouting. carpet. seal coat etc. should be done step by step. The contractor should secure approval from the site engineer after every stage and before starting the work of the next stage.
PROCUREMENT OF MATERIAL
The road contractor should provide all the materials required for the above-mentioned works like rubble for soling, metal, bitumen, etc. at no extra cost.
Stacking and proper use of the material is the contractor’s responsibility. responsible for any loss or theft of the material brought by the road contractor agreement for all construction activities.
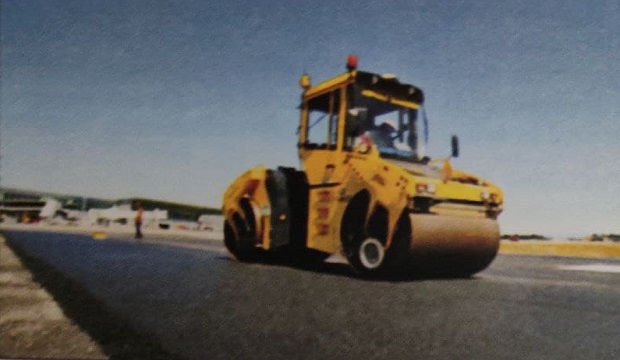
ROAD LEVELS
The labour contractor shall take all the levels, slopes camber of the road section, the chamber at the end section, necessary curvature details at turning, etc. as per the requirement of the drawing details from the site engineer.
N.O.C.
The labour contractor should take N.O.C. from the site engineer for each and every material supplied, as per the specifications.
CONSUMPTION OF BITUMEN
The road the contractor must take the weight of the bitumen browser.
before and after the grouting work, to prove. the minimum required consumption of bitumen in each coat. e.g. in grouting 2.75 kg/ sq.m.
MAINTENANCE
The road contractor should carry out the maintenance and repairs of road surfaces for a period of six months after completion of work free of cost.
SPECIFICATION OF MATERIAL
Specification of material should meet all requirements of the I.S. Code.
MODE OF MEASUREMENT, SCHEDULE OF RATES AND DETAILS OF PAYMENT SCHEDULE
The above terms & conditions should be finalized at the time of the agreement.
10. AGREEMENT LANDSCAPING WORK CONTRACTOR
Landscaping work contracts can be given on a lump sum basis or area basis, with material and labour or only on labour basis.
SCOPE OF WORK
The levelling, cleaning of the area marked for garden development, proper planning in the planting of different types of bushes, trees, watering of plants, providing fertilizers, maintaining them till growth, providing men and material for required landscaping area, developing lawns wherever required by bringing sprinkler, lawn movers, etc.

LEVELLING OF THE GROUND
The garden the contractor should carry out the soi dressing and ground levelling for developing the lawn.
TOOLS AND MACHENERY
Garden The contractor should bring all the tools, e.g. ghamelas, phawda, tikav, and other tools and plants required for daily work at his own cost. He should supply the bushes, trees, and grass with the manures, red soil, etc. bamboo supports for small plants at his own cost.
EMPLOYING LABOUR FORCE
The garden contractor should employ an experienced gardener for the continuous supervision of development works for a period of six months, at no extra cost.
NURSERY DEVELOPMENT
Along with the ongoing development work, the garden contractor should also develop a small nursery from where plants can be used for gardening purposes, at no extra cost.
SCHEDULE OF RATES
Schedule of rates, mode of measurements, and other terms and conditions are normally finalized at the time of the actual agreement mutually with the contract agreement for all construction activities.
Also, Read This.