Mix design concrete procedure has two objectives. One to achieve the minimum required strength and two to prepare the concrete in the most economical manner. Cost-wise, all concrete depends primarily on two factors, namely the cost of labor and the cost of material.
Labor cost includes form-work, batching, mixing, transporting, and curing, with slight variations between good and bad quality concrete.
Therefore, saving on the use of cement with consistent strength and durability is advisable.
Mix Design Concrete Calculations Pdf Download Link Below
This is already an index of the coarseness and fineness of the material. F.M. is an empirical factor, obtained by adding the cumulative percentages of aggregates retained on each of the standard sieves ranging from 80mm-150 microns and dividing this sum by an arbitrary number 100. The larger the figure, the coarser the material.
2. SIEVE ANALYSIS
This is the process for dividing the sample of aggregate into various fractions; each consisting of particles of the same size. Sieve analysis is conducted to determine the particle size distribution in a sample of aggregate, also called gradation.
The following 1.S. sieve sizes are generally used for sieve analysis, 80mm, 63mm, 40mm, 25mm, 20mm, 16mm, 12.5mm, and 10mm for coarse aggregates.
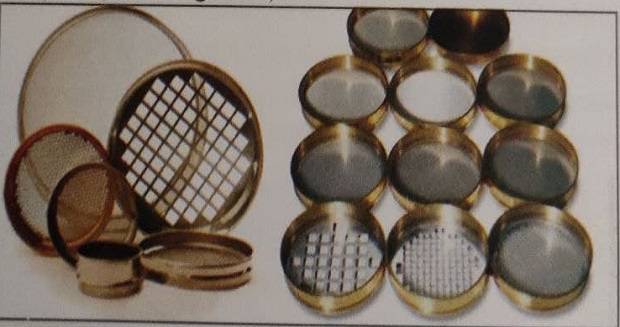
4.75mm, 2.36mm, 1.18mm, 600micron, 300micron, 150micron for fine aggregates.
The sieve analysis should be conducted and the results tabulated in the following format.
In achieving the required strength of the concrete mix, the water-cement ration ratio plays an important role. The strength of the mix decreases as the W/C ratio increases. The relation between the W/C ratio and the strength of concrete is shown.
So, in mixed design, W/C ratio should also be designed to achieve the required compression strength. At the same time remember that, when the water-cement ratio, the ratio is below the practical limit, the strength of the concrete falls rapidly due to the formation of air voids.
To achieve the desired proportion for concrete of the required grade, the considered on an average basis, (as per the materials available in Pune).
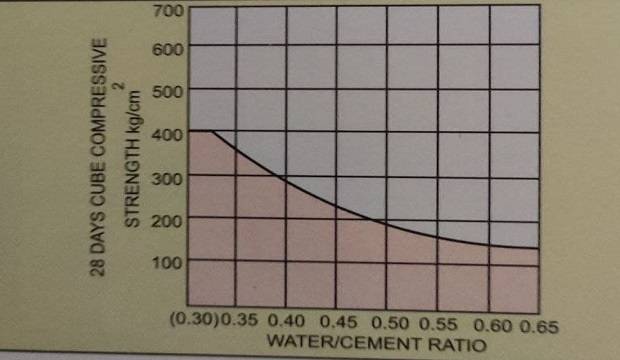
Sand available in & around Pune requires few changes of proportion, considering the following practical assumptions.
- Bulkage of sand 10% to 15%.
- Oversize particles in the sand above 4.75mm are 10% to 15%.
- Absence of fine particles in the sand below 600 microns.
TO ACHIEVE THE DESIRED PROPORTION OF MIX DESIGN AGGREGATE
90 liters (3.2 c.ft.) of 20mm (3/4″) metal 45 liters (1.6 c.ft.) of 12.5mm (1/2″) metal. Total of 135 liters.
- 70 liters of oven-dry sand is required
- Accounting for 15% bulkage 70 + 10.5 = 80.5 liters
- Accounting for 10% oversize particles 80.5 + 8.50 = 89.00 liters
- These 8.5 liters get added to coarse aggregate.
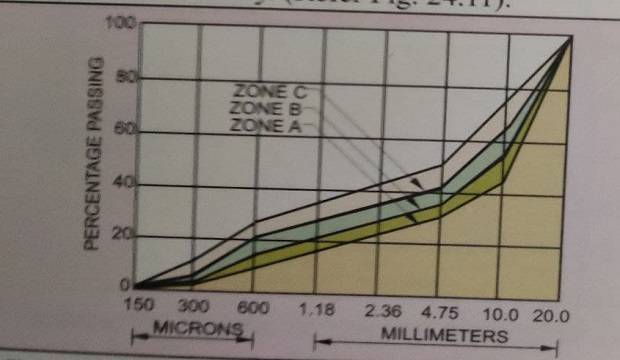
STONE DUST
10 liters of stone dust is recommended. It gets, absorbed volumetrically and does not increase the quantity of sand.
Hence the recommended size of farma and quantity of the material is.
Farma 30cm x 38cm x 30cm = 1.25 c.ft. (1′.00 x 1′.3″ x l’.00)
- Sand
- 2 farmas (full) &
- 1 farma (half)
Metal – 4 farmas (fill 1″ less)
Cement- 1 bag
Again, as per visual acceptance of the required workability, decide which material is to be taken full or as required.
Thus, the design M15 grade mix is arrived as under.
MAIN FACTOR AFFECTING THE PROPERTIES OF MIX DESIGN CONCRETE
The compressive strength of concrete is one of its most important and useful properties. A number of factors affect the above properties of concrete.
This gives the compressive strengths of M15 grade concrete i.e. 15N/mm2 (150kg/cm2) after 28 days of curing.
SR No
|
INGREDIENTS
|
ACTUAL VOLUME
|
EFFECTIVE VOLUME
|
1
|
Cement 1.25 c.ft(35 ltr)
|
1 Bag (35 ltr)
|
35 ltr.
|
2
|
Sand
|
89 ltr. (3.15 c.ft.)
|
70 ltr.
|
3
|
Stone Dust
|
10 ltr.
|
Nil
|
4
|
Coarse aggregate
20mm (3/4″)
15mm (1/2″)
|
90 ltr. (3.2 c.ft.)
45 ltr. (1.6 c.ft)
|
140 ltr.
|
Hence Proportions
|
1:2.54:3.85
|
1:2:4
|
1. W/C RATIO (WATER CEMENT RATIO)
The strength of concrete depends primarily upon the strength of the cement paste.
The strength of cement paste depends on the dilution of the paste i.e., the strength of the paste increases with cement and decreases with air and water content. The compaction of concrete also plays an important role in achieving the desired strength of concrete.
The percentage of gain in strength with the age of the concrete varies for various W/C ratios.
Normally, a 0.55 W/C ratio is used for practical workability.
For workable concrete that can be compacted properly and with ease, W/C ratio has to be a little more than what is needed theoretically. Note that although the W/C ratio is a little higher, the strength of concrete may be more if compaction is good.
The age of cement directly affects its compressive strength. If the cement is stored for a long period, it’s compressive strength reduces considerably.
The following table shows the percentage reduction in strength.
Period of storage of cement | Expected reduction in strength at 28 days |
Fresh | 0% |
3 Months | 20% |
6 Months | 30% |
1 Year | 40% |
2 Year | 50% |
Reduction in cement strength due to storage
- Reduction in strength of cement directly related to Age of cement.
- In general, stored cement loses its strength gradually, with time.
3. GRADING OF THE MATERIALS
Aggregate comprises about 85 percent volume of mass concrete. The way particles of aggregate fit together in the mix, influenced by the gradation has an important effect on the workability of fresh concrete and the properties of hardened concrete.
For producing workable concrete, with the minimum practical W/C ratio, good gradation of aggregates is necessary.
Good grading implies that a sample of aggregate contains all standard fractions of aggregate in the required proportion so that the sample contains minimum voids.
Up to a limit, an increase in the cement content increases the strength of the concrete point, an increase in the cement content can even decrease the strength of the concrete.
Curing occupies a place of increasing importance. as the demand for high-quality concrete increases. It is accepted that the quality of concrete indicates an all-around improvement with efficient and uninterrupted curing. When curing is neglected in the early period of hydration, the quality of concrete experiences a somewhat irreparable loss.
The use of admixtures influences the workability and strength of concrete. The concrete can be made more workable at a low W/C ratio, with the help of plasticizers and superplasticizers. With a low W/C ratio and higher workability, it can be compacted easily to yield better strength.
MIXING OF CONCRETE
The main object of the mix design concrete ration procedure is to coat the surface of all aggregate particles with the cement paste and to blend all the ingredients of the concrete into a uniform mass.
- Hand mixing
- By using mixers
- Check the platform before mixing it. At the time of mixing, ensure that no cement slurry flows away. Use M.S. trays if a concrete platform is not available.
- Check the “depo” or the proportion of sand, metal, and cement for one bag mix. Measurement should be taken by farma only.
- Prepare one bag mix at a time.
- Spread the cement over the aggregate. Dry materials are mixed by turning them over, from one end to another, and cutting with a shovel until the mix appears uniform.
- Turning is done three times for dry mix material, for proper mixing.
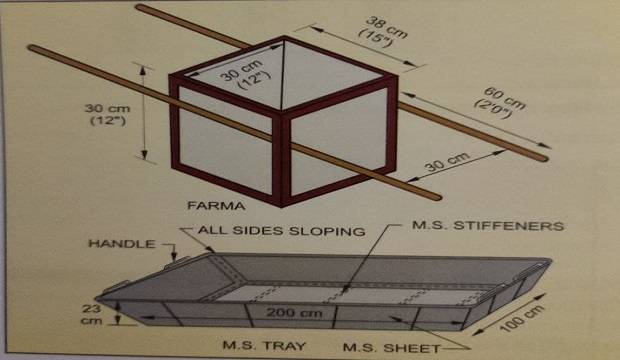
- Make a pond required size in dry material for water.
- Add an approx, quantity of water slowly to the dry mix, using a bucket. Check the capacity of the bucket.
- After adding water, mix all the materials until a uniform color and consistency appear.
- After visual inspection, if the color and consistency of the concrete does not seem right, add 10% more cement in the same mix.
- Mix the wet concrete thoroughly.
Machine mixing is faster and cheaper than hand mixing. It generally produces more strength and better workability.
Types of Mixers
- Tilting mixer
- Non-tilting mixer
- Pan mixer
A tilting mixer is used more often. The following points should be noted while using the tilting mixer.
- Clean the hopper first.
- Place the coarse aggregates first in the hopper, followed by sand and cement.
- Check if the correct quantities of cement and aggregates are loaded in the hopper or not.
Raise the hopper to discharge the material into the rotating drum.
Add. the correct amount of water in the drum using a bucket cylinder.
The period of mixing in the rotating drum should be 1-2 minutes after all the material has been loaded.
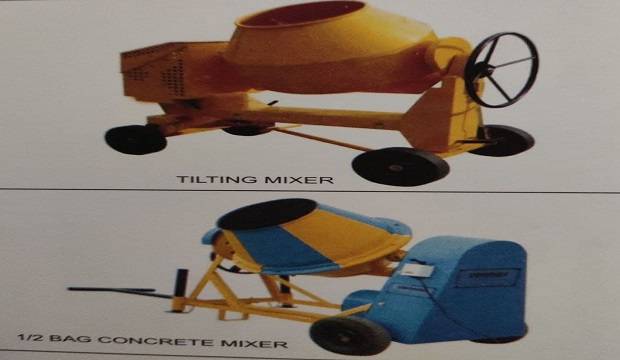
ADVANTAGES OF MACHINE MIXING CONCRETE
- The water-cement ratio can be controlled easily in machine mixing.
- All materials like cement, sand, metal, etc. can be mixed properly due to the rotation of the drum.
- Allows ease of control over mixing, i.e. up to the required color and consistency.
- Wastage of cement sand metal can be reduced with the hopper.
- For larger concreting works, the strength of labour is reduced.
- With proper mixing and visual inspection of the concrete, good strength can be achieved, with a lesser W/C ratio.
PRECAUTIONS TO BE TAKEN BEFORE AND DURING CONCRETING BY MIXER
- The mixer should be set up on firm and level ground.
- Check the rope of the hopper.
- Check the water in the radiator of the engine.
- Check the quantity of fuel.
- The speed of the machine should be uniform.
- Ensure the required number of blades in the drum, i.e., a minimum of 3 nos.
- Any worn-out or bent blades in the drum should be replaced immediately.
- The drum of the mixer should not be overloaded.
- The mixer should run for one and a half to two minutes for each bag of cement, with the rotation of the drum varying from 15 to 20 revolutions per minute.
- Ensure that the drum and the hopper are completely empty.
- Ensure that there are proper vibrations to the hopper.
- While loading the material, coarse aggregates are generally placed at the bottom, cement in the center, and fine aggregates on top.
- Check the lubricants in bearings, gear wheels & gearboxes before using.
CARE TO BE TAKEN WHILE HANDLING MIXER CONCRETE
- The revolving drum should be cleaned every day after concreting, by adding coarse aggregate and water and then revolving it for two minutes, and then washing it out.
- When not in use, the drum should be covered with a plastic cover.
- Worn-out and bent blades should be replaced immediately.
- Oil grease the joints and parts at least once a month.
- Check the air pressure in the tires.
- When not in use, run the mixer for some time, at least once a week.
concrete mix design ratio
- M5 concrete ratio: 1:5:10
- M7.5 concrete ratio: 1:4:8
- M10 concrete ratio: 1:3:9
- M15 concrete ratio: 1:2:4
- M20 concrete ratio: 1:1.5:3
- M25 concrete ratio: 1:1:2
- M30 concrete ratio: Design Mix
- M35 concrete ratio: Design Mix
- M40 concrete ratio: Design Mix
- M45 concrete ratio: Design Mix
- M50 concrete ratio: Design Mix
- M55 concrete ratio: Design Mix
- M60 concrete ratio: Design Mix
- M65 concrete ratio: Design Mix
- M70 concrete ratio: Design Mix
Also, Read This
IF YOU LIKE THIS POST MIX DESIGN CONCRETE RATION PROCEDURE | DIFFERENT GRADES OF CONCRETE LIKE THIS GETTING GOOD INFORMATION SO PLEASE THIS POST SOCIAL NETWORK EXAMPLE FACEBOOK, TWITTER SOCIAL MEDIA SITES SHARE IT.